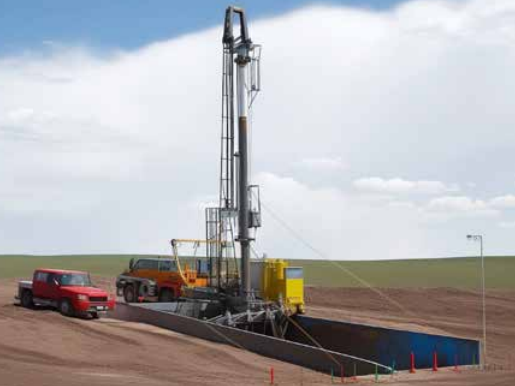
随着当代科技的进 步, 数 字 化 技 术 已融入到了各行 各 业。 在 钻 头 制 造和油气钻井领域,数字孪生(映 射)技术结合钻头内传感器等创 新成果大大缩短了产品迭代周 期,可有效的帮助钻头制造商和 钻井作业商更快地将适用的钻头 投送到现场。 在帮助钻井作业商为给定的 井段选择合适的钻头时,钻头服 务公司通常需要做很多工作。
首 先,需要与作业商合作,以了解 该井段的钻井计划。其次,还需 要测量待钻岩层的动力学性质, 这通常是通过作业商所提供的岩 石强度数据来完成的。另外,为 了帮助钻井作业商实现其目标, 还需要确定给定钻头结构和给定 的井可能需要的定制量的多少。 通常,他们必须应用模拟软件来 收集有关钻头潜在井下性能的多 个方面的信息。这之后通常还会 进行现场测试,而有时却会产生 与模拟不同的结果,让大家不得 不重新进行设计。 除了管理这类变量的挑战以 外,钻头制造商还在不断寻找各 种方法来突破其产品性能的极限, 因为他们认识到,钻井作业商的 恒定目标就是不断寻求以更快的 速度钻到更深的井下目标深度。 国民油井(NOV)公司的钻 头生产管理人员明确表示,由于 当今钻头行业竞争非常激烈,如 果你不努力超越自己之前的产品 性能,你很快就会被取代。他们 认为,公司必须不断超越自我, 不断改进自身钻头的钻井性能。 如果你不这样做,别的公司就会 这样做。
随着世界各地钻井活动的持 续增加,即使是微小的性能改进 也至关重要。贝克休斯公司钻头 产品生产线经理表示,其客户很 多时候都在寻求快速解决方案, 而该公司的目标则是找到最佳解 决方案,将钻头的性能提升到客 户所需的水平,并以最快的速度 实现这一目标。他认为,该公司 对所钻地层的专业知识、对钻头 性能的理解以及为提供最佳结果 所需的技术都很专业,所有这些 对整个钻头选型过程都非常重要。 下面阐述一下美国几家主要 钻头制造商(贝克休斯、哈里伯 顿和国民油井公司)是如何运用 增强模拟软件改善其钻头服务的。 更好的软件不仅可以更好地了解 给定钻头与目标岩层的相互作用, 还可以缩短钻头设计和现场测试 所需的时间,使钻井作业商能够 更快地将钻头投送到现场,从而 尽快开始钻井和生产。
数字孪生技术
美国贝克休斯公司十分注重 数字孪生(映射)技术的应用。 其钻头钻井模拟软件可以创建钻 头和目标地层的数字孪生(映射) 影像,然后再应用专有的切削齿 力学模型来评估切削齿及钻头体 与岩石之间的相互作用。可以对钻井作业商的特定性能限制挑战 进行建模,以找到可定制的解决 方案。 与钻井中的大多数其他过程 一样,各公司一直在努力提高钻 头选型过程的效率。贝克休斯公 司可提供各种工具,以帮助钻井 作业商找到适合其具体钻井应用 领域的钻头。该公司在其位于德 克萨斯州 Woodlands 的工作地点 有一台地面钻机,可以对全尺寸 钻头进行模拟钻探试验。它还配 有一个压力容器,可以用岩芯模 拟井下环境中的各种钻井条件。
然而,为了简化流程,同时 仍能提供精确的钻头性能分析, 贝克休斯公司表示,该公司不仅 在继续投资于更好的软件,同时 还在寻找各种方法以更好地利用 来自其各种产品系列的数十年的 现场数据。 虽然公司的客户正在钻进更 具挑战性的岩性,但在钻头选型 过程中,公司知道能够提供什么 样的钻头产品,以及如何设计更 好的钻头来解决非常具体的钻井 挑战。公司可以缩短设计过程, 因为其工程技术人员了解其钻头 技术在井下的表现。
贝克休斯公司钻头设计过程 中的关键部分之一是其专有的钻 头钻井模拟软件,该软件可以创 建钻头和目标地层的数字孪生(映 像)。然后,它使用专有的切削 齿力学模型来评估切削齿和钻头 体与岩石之间的相互作用。该软 件可基于客户输入来建模钻井应 用中的性能限制挑战,进而评估 各种设计概念和可定制解决方案 的性能,这些可以是从地层变化 到优化固井浮动设备的钻出作业 的任何内容。 用户输入井身参数和岩石属 性后,软件进行模拟,可以确定 特定钻头设计的钻井行为,以预 测切削结构的进攻性和载荷条件。 这种类型的数字孪生能力允许在 建模钻头行为时具有更大的灵活 性,因为它还可以使用以前的数 字孪生数据,根据类似岩层的性 能和类似的钻头设计进行预测。
这种能力为贝克休斯公司提 供了更全面地了解钻头工况的可 能。在某些情况下,拥有数字孪 生映像会导致需要更少的甚至不 需要现场测试,从而将产品迭代 周期缩短几天或甚至几周。 由于贝克休斯公司创建了这 些模型,构建了数字孪生映像, 并建立了一个模拟数据库,所以 可以更快地回答客户的各种问题, 因为公司可以采用其之前已经建 立的模型,并对其进行修改,以 满足当前的具体需求。因为已经 做了很多前期工作,使得整个过 程都得到了简化。
贝 克休斯公司表示,虽然该 公司目前仍然进行产品的现场测 试,但发现一些长期客户现在更 喜欢使用数字孪生技术来代替现 场测试。然而,这种方法需要客 户和供应商之间有更高层次的相 互信任。公司曾花费很多时间根据过去的现场数据和实验室数据 校准其数字能力,而当将这种能 力置于公司与客户间牢固的关系 中后,就意味着双方可以真正地 共同努力去简化钻头选型流程。 在某些情况下,数字技术能 够有效地帮助钻井作业商在不需 要现场测试的情况下创下钻头钻 井性能记录。例如,在 2021 年, 一家公司在二叠纪盆地钻进 12¼ 英 寸 中 间 井 段 时, 其 机 械 钻 速 (ROP)达到了上限。通过计算 机模拟,贝克休斯公司确定了切 削齿是主要的 ROP 限制因素,然 后便在实验室测试了不同的切削 齿及其在钻头表面的布齿位置。 最终,该公司推荐采用了 Prism 异形切削齿技术 的 Dynamus 钻 头,因为模拟结果表明,在被钻井 段的韧性带压页岩地层中,Prism 切削齿上的点载荷是提高机械钻 速的理想选择。 在现场,使用带 Prism 切削 齿的 Dynamus 钻头在 16.3 小时 内 从 1405 英 尺 钻 至 5200 英 尺 的整个中间段,平均机械钻速为 232.8 英尺 / 小时。
根据贝克休斯 公司的统计,这比钻井作业商的 目标高出了 37%,甚至创下了该 井段的钻井记录。 休斯公司表示,一旦将钻头 设计和现场数据输入系统,其数 字孪生建模的下一步便是应用机 器学习方法使数字孪生模型的构 建实现自动化。 休斯公司在运用数字技术辅 助钻头选型的成长过程是这样的, 其前期许多数字化工作都集中在 手动创建模型和构建数字孪生(映 像)上,但随着时间的推移,公 司已经建立了一个模拟库,这意 味着该公司可以有一个更快的过 程,由于已经做了很多前期工作, 所以可以调整和改进以前的模型, 以帮助构建新的模型。自动化可 以帮助该公司进一步减少调试时 间,且公司正致力于进一步加快 这一进程。
来自于钻头内传感器
哈里伯顿公司认为,来自于 钻头内传感器的各井下数据更直 接且更真实,该公司于 2020 年推 出的 Cerebro Force 钻头内传感 器可以直接在钻头上采集钻压、 扭矩和弯曲方面的测量值,使该 公司能够绘制出钻头真实的井下 运动图。 哈里伯顿公司此前依靠在地 面采集的数据来进行钻头设计,但 在 2020 年推出其 Cerebro Force 钻头传感器以后,公司便可以更 好地了解和记录钻头在每一口井 中的运动模式。 Cerebro Force 钻 头 传 感 器 可直接在钻头上获取钻压、扭矩 和弯曲测量值,使该公司能够绘 制出钻头的井下运动和任何相关 的钻井功能障碍。在改进未来的 钻头设计时,这是非常有价值的。 哈里伯顿公司的战略业务经 理 表 示,Cerebro Force 钻 头 传 感器的主要功能是了解地下情况。 地面数据是在距离钻头数千英尺 以外的地方收集的,但钻头内传 感则使技术人员能够从井下的角 度看到究竟发生了什么事情,因 此能够更清楚地了解钻头与岩石 界面的情况,并为钻头设计提供 更好参考数据。目前该公司正在 研究横向振动、轴向振动、粘滑 和回旋发生的位置,然后将这些 信息与钻头设计、选型和具体的 钻井作业相结合。
在 威 利 斯 顿(Williston) 盆地的一个项目中,来自钻头内 传感器的数据帮助该公司设计了 一款 Cerebro 钻头。现场测试数 据显示,当滚动元件与地层接触 时,钻头获得了最快的机械钻速 (ROP),同时使扭矩最小化。 当滚动元件啮合时,扭矩被最小 化,从而提高了机械钻速。然而, 传感器数据也显示,在每次测试 中,滚动元件处于啮合状态的比 例很小。 哈里伯顿公司设计人员随后 降低了滚动元件啮合时的切削深 度,这一举措使滚动元件能够在 钻进过程中与地层啮合的比例更 大,并因而提高了机械钻速。改 进前的最高机械钻速为 113.0 英 尺 / 小时,而改进后的最大机械钻速则为 160.2 英尺 / 小时。 最近,哈里伯顿公司在其钻 头设计工具箱中添加了另一个十 分有用的工具——Oculus,这是 一个自动化软件程序,可作为钻 头钝化等级的评定系统。
该软件 于 2021 年推出,使用机器学习算 法捕捉钻头上单个切削齿的精确 的钝度信息。该程序可分析将钻 头从井中取出后拍摄的图像,并 将数据编入到云数据库中,然后, 它会自动对每颗切削齿的磨损程 度进行分级。 通过自动化钝度分级过程, 消除了人工检验员目视检查的主 观性,使哈里伯顿公司能够获得 更精确的钻头钝度测量和分类。 这使得包括在设计过程的测试阶 段,对使用大量钻头上的钝度分 析数据也变得更加容易。 哈里伯顿公司之前评估钻头 时,即使应用 IADC 代码,也会 不可避免的带有一些主观性。比 如某个人可能会将钻头评为 1-2 级,另一个人可能评为 1-3 级, 而换一个人则可能会评定为 2-3 级。 而 通 过 应 用 Oculus 程 序, 为每颗切削齿拍摄数字图像,将 其输入系统,并给它一个更具体、 更客观的等级,这样就可以把一 些非常主观的见解转化为客观准 确的数据。 哈里伯顿公司在的全球服务 中心都利用 Oculus 软件进行固 定切削齿的钝度分析。
该公司于 2022 年推出了其最新的 Hedron 固定切削齿平台,将 Oculus 作 为更高效、更耐用的 PDC 钻头设 计的关键组件。 在 去 年 的 一 个 项 目 中, 哈 里伯顿公司与中东的一家定向钻 井公司合作,该钻井公司希望能 够 提 高 机 械 钻 速(ROP)。 哈 里伯顿公司利用类似地层的历史 数 据, 选 择 了 在 肩 部 区 域 使 用 带 有 Geometrix 形 状 切 削 齿 的 Hedron PDC 钻头作为起点,在 随后的模拟和测试中,发现减小 金刚石体积会对钻头的稳定性产 生负面影响,并加剧了地层过渡 期间钻头肩部出现的轻微断裂。 这一发现促使哈里伯顿公司寻找 改变钻头设计概念的方法,以提 高切削齿的效率,并将不稳定的 可能性降至最低。 根据 Oculus 系统提供的数 据,该公司保持了与参考钻头相 同的轮廓和切削齿位置,但引入 了最佳的后倾角方案,以提高效 率,并降低冲击损坏的可能性。
在哈里伯顿公司的专有建模软件 中进行测试后,在调整后倾角状 态之前,对锥形面、鼻部和肩部 都进行了检查。钻头的锥形面区 域没有变化,因为在钻头设计软 件中进行的设计模拟表明,这种 变化可能会导致锥形面切削齿过 度啮合,从而加剧振动水平,并 增加产生井下功能障碍的可能性。 在建模软件的最后一次测试 中,与参考钻头相比,钻头效率 提高了 26%。然后,对改进后的 钻头进行了现场测试,其机械钻 速(ROP)达到了 81.2 英尺 / 小时, 比之前的 69.6 英尺 / 小时的记录 高出了近 12 英尺 / 小时。 Oculus 系统在很大程度上帮 助哈里伯顿公司更好地了解了切 削齿在许多不同钻井应用中的表 现,无论是磨损、冲击环境还是 高热环境,使得该公司能够在向 客户介绍其新型钻头技术时做出 更好的选择。
提高钻头的适配性
国民油井(NOV)公司则非 常注重在提供其高性能钻头产品 时与钻井作业商的有机合作与协 调。该公司一直专注于改进切削 齿的粉料牌号和形状,以帮助钻 井作业商提高钻井性能。公司于 去年推出的新型 ION+5DX 切削 齿就是一个例子,其特点是齿的 工作脊能够承受突然的冲击,同 时向所钻地层施加高的压缩载荷。 NOV 公司擅长应用其丰富的 软件程序来帮助钻井作业商选取 合适的钻头。Terra-Scope 是该 公司长期以来所应用的井下地震 监测系统,它可以分析岩石强度 数据,并输出目标地层最可能的 失效机制。例如,它可以确定钻 头是否更有可能在应力作用下失效(这需要 3D 形状的切削齿)或 者更有可能在应变作用下失效(这 就需要全圆形切削齿)。
然后, 该公司使用其 Orbits 软件进行模 拟,以检验某种给定钻头设计在 钻井作业商指定的岩石属性下的 性能。 NOV 公 司 认 为, 尽 管 Terra-Scope 和 Orbits 等 软 件 很复杂,但现场工程师仍需要做 很多工作来梳理钻机上可能发生 的或钻井时钻头会发生的所有不 同情况,而查看所有可用数据并 提出合理的建议还需要大量的协 调工作。 这 就 是 NOV 工 程 技 术 人 员 一直认为钻头的选型过程实际上 就是钻头商家与钻井作业商必须 紧密合作的根本原因。例如,在 Orbits 模拟程序中选择将要使用 的钻头轮廓通常是一个反复的过 程,需要由作业者提供其性能目 标,并概述其在前几次钻进地层 时识别出的限制因素。可能需要 两到三次的产品更替才能为钻井 作业商提供正确的钻头轮廓,使 其钻井应用的价值最大化。
尤其是在二叠纪这样的盆地, 钻井作业员会在任何岩层中钻各 种尺寸的井,就更加需要对钻头 设计进行个性化定制。在这些情 况下,最初的现场测试通常被证 明是非常有价值的。虽然模拟软 件能够很好地预估钻头的性能, 例如,可为各种井下振动和钻头 的攻击性提供潜在理论,但通常 仍需要进行实际的钻进,以更清 楚地了解影响钻头性能的具体因 素。例如,NOV 在其模拟软件中 运行附加应用程序,用以分析发 生钻头回旋和粘滑等井下功能障 碍的可能性,但编程到这些附加 程序中的模型却只能提供大致的 估计效果。 尽管多年来钻头选型的过程 一直保持相对不变,但 NOV 公司 表示,其取得最大进展的地方是 应用钻头提高钻井作业商的钻井 性能。这包括利用从以前的钻头 设计中获得的知识,在未来的项 目中提高钻井效率——特别是, 该公司一直致力于改善切削齿选 材牌号和切削齿形状,以帮助使 钻头更加稳定并提高其耐用性。 NOV 公司认为,钻井作业商 节省资金的方法是减少钻井天数。 单个井段的机械钻速(ROP)已 经达到了一个临界点,所以现在 该公司正在研究如何用相同的钻 头钻进更多的井段,这样就不必 再为同样的钻井工具花费资金了。
这对切削齿来说是一个独特的挑 战,因为这样一来在同一趟钻进 中要经历不同类型的岩石破坏。 该公司正在研究如何建造一个合 理的切削齿布局阵列,它可以使 钻头穿过研磨性页岩、回到研磨 性砂岩、然后再回到页岩中去—— 所有这些都在一个层段内进行, 而不需要用不同的钻头进行单独 的钻进。 2022 年 3 月,NOV 公 司 推 出了 ION+5DX 切削齿,该切削 齿包含一个工作脊,可以承受突 然的冲击,同时向地层施加高的 压缩载荷。应用这种切削齿的目 标是最大限度地减少冲击损伤, 同时最大限度地提高机械钻速。 该公司表示,与普通商用切削齿 的平均值相比,5DX 齿的材料韧 性(即材料在断裂前每单位体积 可以吸收的能量)提高了 60%。 该公司研发切削齿的团队一 直在研究新的切削齿材料牌号, 并不断改善切削齿的形状和布置。 通过应用更加耐冲击的切削齿, 可以在设计方面更加积极,使钻 头更具进攻性,从而帮助公司的 钻井客户超越其目标。如果钻井 作业商能够在 24 小时内钻 9000 英尺的水平段,该公司自信能够 帮助其在未来更短的时间内钻进 同样的距离。 时代在发展,科技在进步。 有理由相信,随着数字化技术应 用的不断深入,包括数字孪生(映 射)技术在内的各种数字化工具 在简化钻头选型、钻头设计和钻 头测试的过程中必将会发挥越来 越广泛和重要的作用。